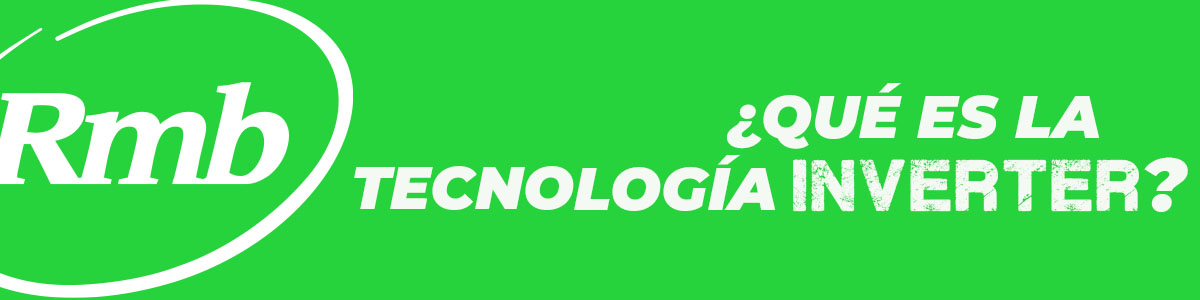
Hemos mencionado ya el principio de soldadura por arco eléctrico, es decir el proceso de soldadura por fusión en el cual la unificación de los metales se obtiene mediante el calor de un arco eléctrico entre un electrodo y pieza a soldar.
Debido a esto, podemos imaginar que hay una estrecha relación entre la corriente eléctrica y el proceso de soldadura. Sin embargo es importante identificar la corriente eléctrica en distintos momentos del proceso, ya que cumplirá diversas funciones:
No es lo mismo, la corriente de alimentación del equipo suministrada por la red eléctrica (sea monofásica o trifásica), que la corriente de soldadura que el operario configura para soldar. Lo que ocurrirá es que esa señal inicial, se irá modificando de acuerdo a la tecnología que tengamos disponible y el tipo de soldadura que sea requerida.
Entonces podemos hablar de tres momentos:
- Una etapa de alimentación o entrada (input),
- Una segunda etapa de transformación de esa señal de entrada.
- Y un tercer paso que es la salida (output) y que involucra a la señal utilizada para soldar.
Para explicar este fenómeno, es necesario tomar como referencia la ya obsoleta tecnología electromagnética, nos referimos a los equipos que trabajan con transformadores a bobinado. En este caso, se contaba con un bobinado primario, que era atravesado por la energía de alimentación, por ejemplo 220V monofásico de corriente alterna. La corriente alterna (CA) es un tipo de corriente eléctrica, en la que la dirección del flujo de electrones va y viene a intervalos regulares o en ciclos. La corriente que fluye por las líneas eléctricas y la electricidad disponible normalmente en las casas procedente de los enchufes de la pared es corriente alterna. En nuestro país, ese “ida y vuelta” se da a razón de 50 ciclos por segundo (es decir, una frecuencia de 50 Hertz).
Es por esto, que el arco de soldadura con este tipo de corriente, tiene cierta inestabilidad. Si bien este proceso ocurre a una velocidad imperceptible, sus efectos se reflejan en la estabilidad de ese arco eléctrico.
Volviendo a la explicación, cuando esta energía atravesaba al bobinado primario, generaban un campo electromagnético que inducía a un bobinado secundario que contaba con características diferentes al primario (cantidad de vueltas de alambre) y lograban establecer un cambio en la relación de voltaje y amperaje (potencia) para lograr valores de voltaje relativamente bajos y amperajes elevados, qué como ya hemos visto, es indispensable para poder soldar.
Dicho en otras palabras, debido a que la energía no puede desaparecer, sino que se transforma, lo que ocurre con los transformadores es lo siguiente:
Si el consumo diseñado para ese equipo, son 2200 Watts, y sabiendo que mi voltaje de entrada es fijo (220V), puedo deducir que mi equipo consumirá 10 A, ya que por ley de ohm Potencia (W) = Voltaje (V) x Amperaje (A), entonces 2200W = 220 V x Amperaje. De ahí que calculamos esos 10 A.
Sin embargo, el soldador cuando compra un equipo, quiere tener un rango de amperaje para poder soldar, por ejemplo entre 30 a 160 A. La única manera de obtener esa variación, es modificando la energía de inducción entre el bobinado primario, y el secundario. Es es básicamente lo que se regulaba con los equipos electromagnéticos. No se amplificaba ni se reducía la potencia, sino que justamente, se transformaba esa relación VxA, de ahí el nombre de “transformadores”
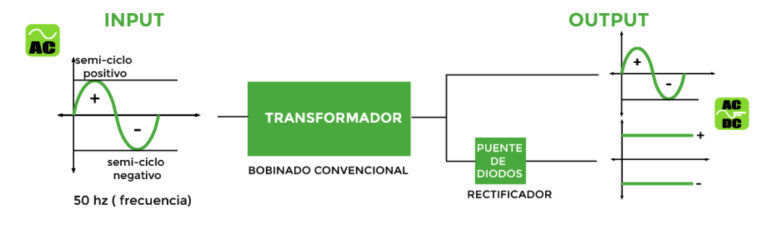
Como vemos en la figura, tenemos una entrada de corriente alterna, un sistema de transformadores convencional como el que describimos anteriormente y podemos tener 2 outputs: Una de corriente alterna sinusoidal, como indica la figura, o una señal continua lograda por medio de un “puente de diodos”. No pretendemos describirlo con detalle, pero podemos decir que a través de la utilización de estos componentes electrónicos, los cuales solamente permiten el paso de la corriente eléctrica en un único sentido, a través de sus dos terminales (ánodo y cátodo), se lograba obtener una señal de corriente continua, la cual es una corriente de intensidad constante en la que el movimiento de las cargas siempre es en el mismo sentido.
Lo que podemos intuir, es que si la corriente tiene un mismo sentido de circulación, el arco de soldadura será más estable y será más fácil soldar.
Habiendo explicado esto, podemos comprender mejor qué ocurre con la tecnología inverter:
Los equipos con tecnología inverter, utilizan componentes electrónicos, (siendo los transistores IGBT unos de los más importantes), para rectificar la corriente alterna de entrada, ya sea monofásica o trifásica, en corriente continua de soldadura.
Está energía pasará a transformarse en AC de alta frecuencia, la cual tiene unos valores entre 20.000 y 50.000Hz.
Entonces es importante romper un mito: La tecnología inverter es un modo de transformar la energía que puede ser aplicado en cualquier proceso de soldadura, MMA, MIG-MAG, TIG, no se limita solo al proceso de electrodo revestido, a pesar de que suele asociarse al término “inverter” con los equipos compactos, livianos utilizados para soldar con electrodo revestido.
El hecho de prescindir de sistemas electromagnéticos como los transformadores bobinados tradicionales, permite lograr equipos de peso y tamaño reducidos, y fundamentalmente con un control más preciso del arco de soldadura.
Por otro lado, al tratarse de un equipo electrónico, está compuesto como decíamos, por componentes electrónicos (hardware), pero a la vez, cuenta con una parte blanda, de programación (software), que le permite al fabricante añadir funciones específicas a los equipos, que facilitan el proceso de soldadura. Estas funciones se explican con detalle en el módulo: Beneficios de las funciones.
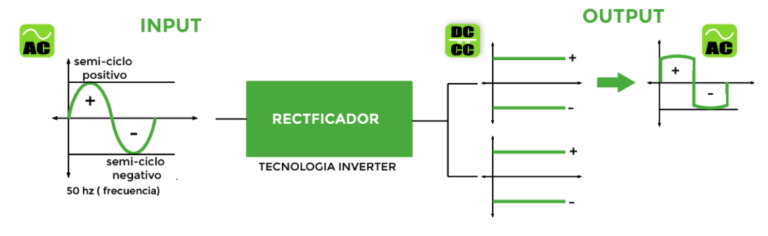
Entonces, los tres momentos de transformación en tecnología inverter serán los indicados en la figura. Ingresa (input) una señal alterna sinusoidal, el paquete de componentes electrónicos lo convierte en corriente continua.
Puede existir un nuevo output, qee se da en el caso de la corriente de soldadura para aluminio. Como ya hemos explicado, el aluminio tiene la particularidad de que el óxido de alúmina que se genera en su capa superficial, tiene un punto de fusión muy por encima del que tiene el aluminio en si, por lo cual se requiere de ese “ida y vuelta” que caracteriza a la corriente alterna, para romper esa película dura y a su vez poder aportar material.
Para ello, para soladuras de este tipo, se vuelve a llevar a cabo una trasformación de la señal continua obtenida en el output, generándose una señal alterna pero de forma cuadrada, y no de forma sinusoidal como estamos acostumbrados.
Esta señal, es más eficiente desde el punto de vista del aprovechamiento energético en cada ciclo, y eso se ve reflejado, en que posee un área mayor bajo la curva, como mostramos a continuación en la figura.
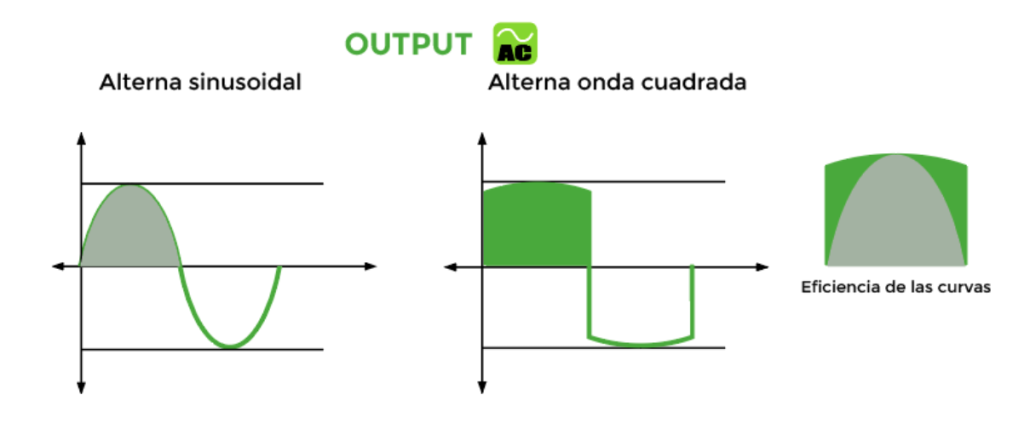
Aunque su nombre parece decir lo contrario, el acero inoxidable también se oxida. Sin embargo, la resistencia a la corrosión de este material se debe a una película ‘pasiva’ de un óxido complejo rico en cromo, que se forma espontáneamente en la superficie del mismo. Éste es el estado normal de las superficies de acero […]
Como ya hemos dicho en secciones anteriores, el calor aportado en la unión es directamente proporcional a la potencia de soldadura e inversamente proporcional al tiempo que permanece ese calor en una zona determinada (velocidad de avance). Dicho de otra manera, debe haber una relación equilibrada entre estas dos variables, ya que una potencia de […]
La resistencia Mecánica de una unión depende principalmente del material de aporte utilizado. Independientemente del proceso de soldadura utilizado, esta es una de las variables mas criticas para lograr una buena soldadura y la ficha técnica permite conocer las características del material a utilizar para poder desarrollar el plan de acción que mejor se adapte […]